Machine Tool Manufacturer of High-Performance Machining Solutions
Modig Machine Tool is a reliable machine tool builder developing, engineering, and manufacturing premium machine tools for high-performance machining in leading industries: aerospace, automotive, energy, construction, and heavy equipment. Our machine tools are equipped with the latest technology to provide optimal performance in cutting, drilling, milling, and turning, and they come with complete automation options.
Horizontal Machining Center
Our horizontal machining centers are built to secure your desired machining times and increase productivity without compromising quality.
Vertical Machining Center
MODIG´s Vertical machining centers are designed to provide unbeatable speed and rigidity, delivering steady performance even at full spindle speed.
Inverted Machining Center
We are proud to display the world’s first inverted machining center and set new standards for productivity, precision, and speed.
Automation Solutions
Robotic machine loading, overhead loading system, Bar feeder, Pallet system, Robotic tool loading and complete automation concepts from MODIG.
Looking for a Machine Tool Builder. Why MODIG?
- Customer focus: MODIG stands out by providing a comprehensive solution that includes problem-solving, customized configuration, testing, training, and technical and customer support.
- Cycle time reduction: MODIG’s machining center is designed to offer fast and efficient cycle times, giving you a competitive edge in your industry.
- Fast return on investment: The return on investment for a MODIG machining solution is typically achieved within 11-18 months.
- Long-lasting values: MODIG provides machining solutions that enhance production efficiency and profitability, delivering long-lasting value.
- Long product life cycle: MODIG machines are built to last, incorporating the latest technology and exceptional quality.
- In-house R&D and manufacturing
Machining Solutions
Our company specializes in building machine tools and machining solutions that offer incredibly short cycle times and remove chips at a record rate. As a result, our machining centers are ideal for manufacturing parts for electric vehicles, aircraft, heavy equipment, doors, windows, and more.
About Modig Machine Tool
MODIG Machine Tool is today led by the third generation MODIG, David Modig, and celebrated as one of the world’s leading machine tool manufacturers of premium performance machining centers. MODIG also provides aftermarket support and complete automation solutions. With over 11,000 machine tools sold worldwide, the MODIG brand is a trusted partner for your business. Every machine tool leaving the plant in Kalmar results from a seamless collaboration between our R&D and the production team.
Tomorrow´s Technology Today
With unique solutions, flexible configurations, and the ability to provide tomorrow’s technology today, we will improve your productivity together.
MODIG Machine Tool has an in-house R&D department that works with the latest technology, mechanics, pneumatics, and hydraulics. We continuously develop and improve our machine tool solutions to secure high accuracy, speed, flexibility, and rigidity.
Machine Tool Builder with Long Traditions
The story of the machine tool manufacturer MODIG starts deep into the forests in the south of Sweden in 1947. The four brothers of Modig founded the company and began to build machines in Virserum, Sweden. When the company’s lathes, universal drills, and machining centers became more well known worldwide, a woman ran the company, something unique for the time. Ulla Modig was an amazing woman, a true source of inspiration and genuine in the famous MODIG family spirit. Time goes by, and when the 2nd generation takes over, Percy Modig, the company reaches excellent success within the aerospace industry.
MODIG Machine Tool has a long history in machine tool manufacturing characterized by many innovations that have shaped the development of machine tools over the years. The introduction of the first computerized machine in 1982 marked the beginning of a new era for the machine tool manufacturer. MODIG turned their focus and left the off-the-shelf devices behind and introduced the first high-speed machining center in the world in 1987. The following year MODIG launched the world’s first extrusion machine with rotary tables, Profile Line, a powerful best-in-class machine with incredible speeds and feeds, making MODIG the company with the most extensive knowledge in extrusion machining today.
Today, the 3rd generation MODIG, David Modig, runs the company and we are still well-known for our technical ingenuity. In recent years, MODIG has set a new standard for machining, first, with the RigiMill, which holds the world record in material removal. Then with the Inverted machining centers, the next generation of machining.
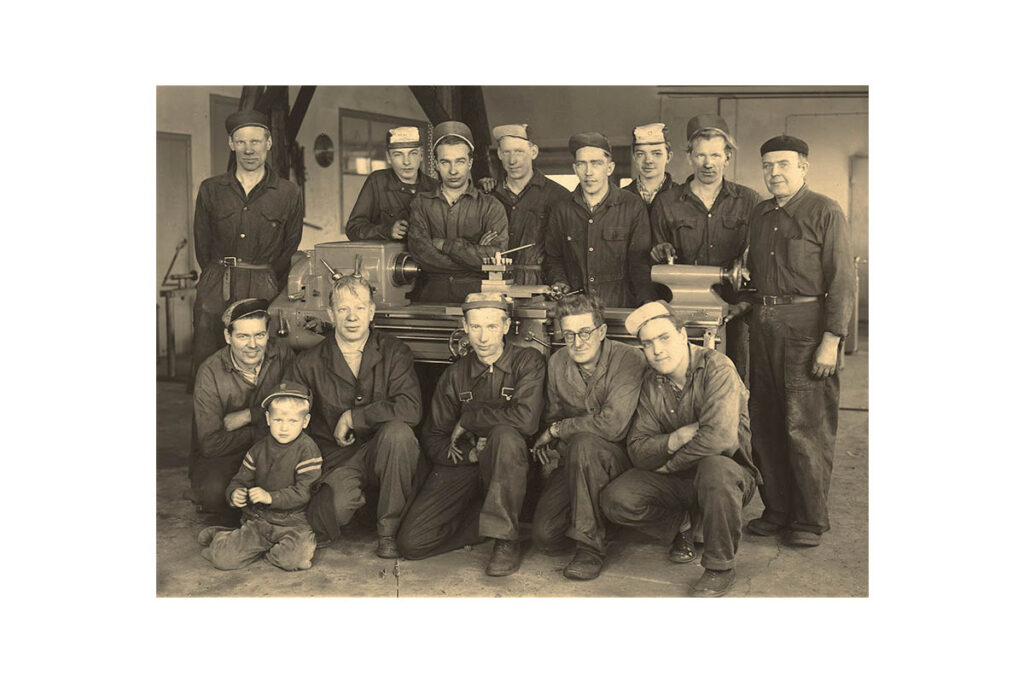
Machining Centers Available with 3, 4, and 5 Axis Configurations
When selecting a CNC machining center, it is important to consider the number of axes required for machining. Modig provides 3-axis, 4-axis, and 5-axis machining options.
In 3-axis machining, the workpiece is fixed in one position, and the spindle can move in three linear axes: X, Y, and Z. This type is suitable for parts that don’t require much detail or depth, commonly used for mechanical parts and tasks like milling slots and drilling pockets. However, it may be less effective for cutting hard-to-reach areas.
4-axis machining adds rotation to the three linear axes, allowing for processing multiple sides of the workpiece in one setup. This reduces the need for multiple configurations and is ideal for tasks like intermittent cutting and engraving curved surfaces, ensuring high quality and precision.
In 5-axis machining, three linear axes and two axes of rotation work simultaneously. This allows for complex surface machining in a single setup. With the additional rotation, a 5-axis machine offers more flexibility and higher precision, making it beneficial for components that require great complexity and accuracy.
Choosing the right machining center depends on the specific requirements of the job and the desired level of productivity and precision.